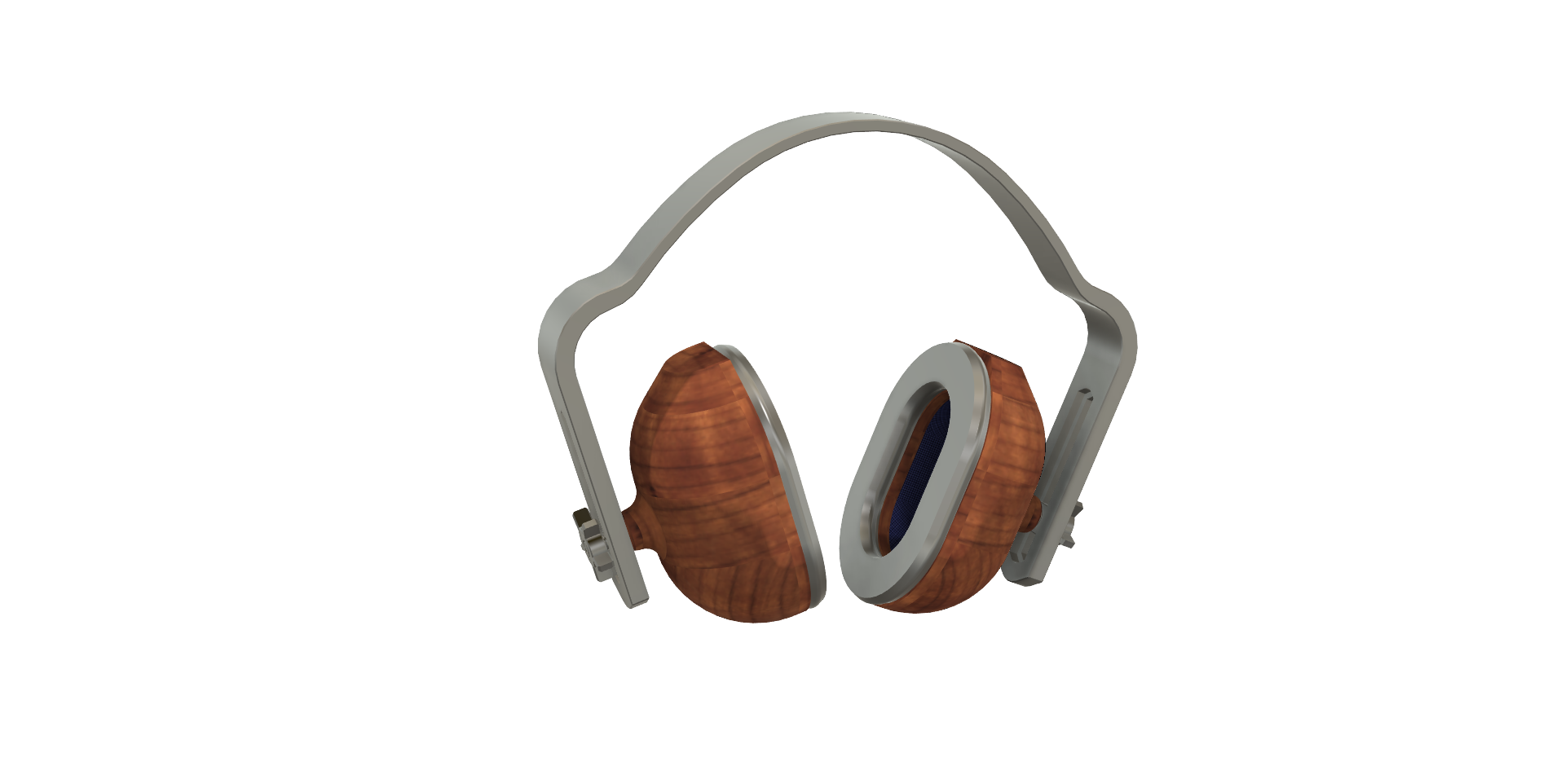
Casque anti-bruit 100% en Impression 3D
Casque, bruit, DIY, Impression 3D
Jean Boulvert
3/10/20255 min lire
Cet article présente l'état d'avancement de notre projet de conception d'un casque anti-bruit 100% réalisable à l'aide d'une imprimante 3D FDM.
CE CASQUE ANTI-BRUIT N'EST PAR CERTIFIE - NE PEUT PAS REMPLACER UN EPI
Vue d'ensemble
Le casque est composé de deux coquilles recouvrant les oreilles et d'un arceau plaquant les coquilles sur la tête.
Les coquilles sont composées de deux coques (sur l'illustration : marron) séparées par un matériau poreux visco-élastique (gris), un matériau poreux (bleu) à l'intérieur de la coquille et d'un joint (gris).
Le joint et le matériau poreux visco-élastique sont à imprimer en TPU, une matière flexible et visco-élastique.
Les autres composants sont à imprimer en PLA ou une autre matière rigide.


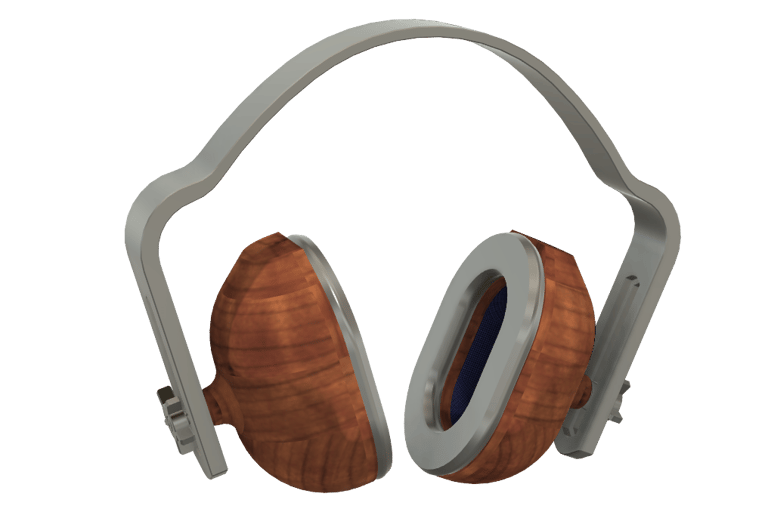
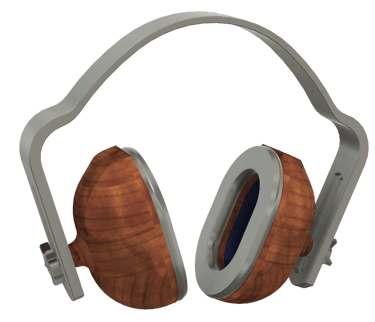
Conception
A. Interface casque - tête
L'étanchéité de l'interface entre le casque et la tête est primordiale pour apporter un isolement acoustique élevé. Il en va d'ailleurs de même avec des bouchons d'oreilles.
Si le montage laisse un espace libre entre le casque et la tête, alors le bruit passera principalement par cet espace libre.
Nous avons des différences de forme et de taille de tête, entre individus. Le casque doit donc pouvoir s'adapter à ces différences vu qu'il n'est pas sur-mesure.
Les coquilles sont liées à l'arceau par des liaisons rotules reliées à une glissère ajustable. Ainsi, lorsqu'elles sont plaquées contre la tête, les coquilles suivent sa forme.
De plus, un joint (gris, en forme de "3") souple permet à la coquille d'épouser la forme de la tête. Habituellement, cette fonction est assurée par une mousse dense. La réalisation à 100% par impression 3D nous a poussé à préférer un joint souple. La barre central du joint glisse entre deux parois de la coque intérieure du casque ce qui permet que le joint soit le plus fin possible une fois le casque plaqué sur les oreilles. Les barres extérieures du joint lui donnent son effet ressort grâce à leur forme en S.
Enfin, pour renforcer l'isolement au niveau du joint, un résonateur poreux (bleu) est placé le long du parcours de l'onde acoustique qui pénètre dans le casque via le coté du joint. C'est le même concept que de mettre une baguette de matériau poreux sur le bord du canal d'une entrée d'air de fenêtres. Cf notre article de blog sur les entrées d'air --> https://sil-et-add.fr/reduire-le-bruit-des-entrees-dair
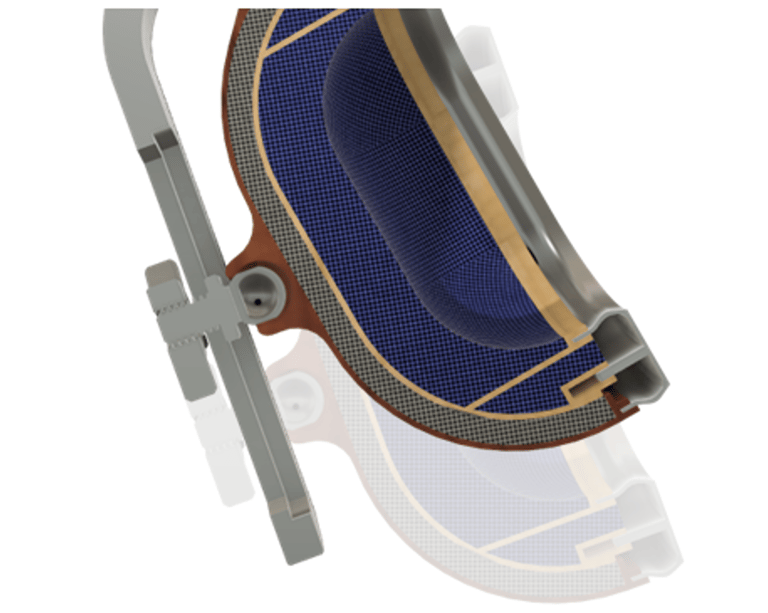
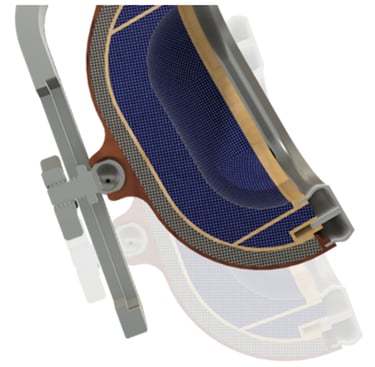
B. Isolement de la coquille
La coquille isole du bruit en appliquant le principe de paroi double. Ce principe est employé dans de nombreuses applications : murs de bâtiments, encapsulation de moteurs etc.
La coquille est donc composée de deux parois / coques pleines (marron) séparées par un matériau poreux à porosité ouverte (gris).
Le matériau poreux entre les deux parois est imprimé en TPU. Cette matière est flexible et visco-élastique. Ainsi, le matériau poreux atténue les résonances acoustiques entre les deux parois grâce à sa résistivité (petits pores) et il atténue les résonances mécaniques des parois grâce à sa visco-élasticité. Par ailleurs, pour améliorer le découplage vibratoire entre la coque intérieure et extérieure, le contact entre le matériau poreux et la coque intérieur est limité à une très faible surface. Celà est rendu possible par un motif très espacé à la surface du matériau poreux.
Enfin, le matériau poreux est imprimé à plat, comme un tissu, pour simplifier son impression.
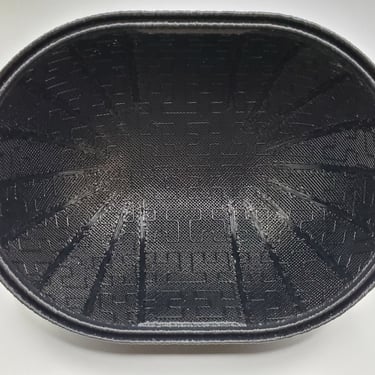
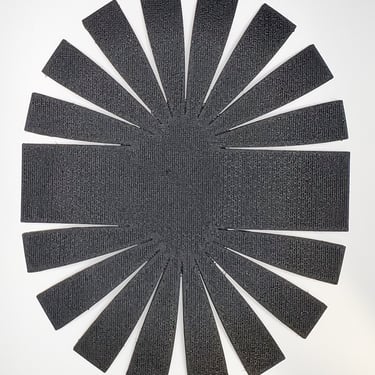
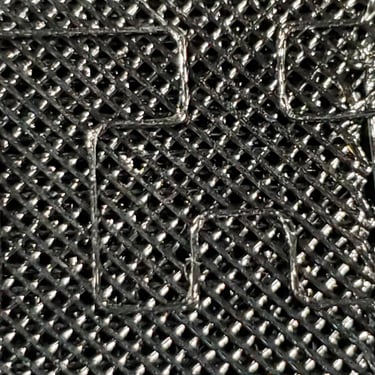
C. Effet "bruit de mer dans un coquillage"
L'intérieur de la coquille est recouverte d'un matériau poreux à porosité ouverte (bleu).
Son rôle est d'atténuer la résonance acoustique de la cavité formée entre la tête et le reste de la coquille grâce aux pertes acoustiques qu'il engendre. Autrement dit, cela revient à mettre de la mousse à l'intérieur d'un coquillage pour ne plus entendre la mer en portant le coquillage à l'oreille.
Pour mieux comprendre ce phénomène, voir notre article de blog --> https://sil-et-add.fr/entendre-la-mer-dans-les-coquillages
Impression 3D par dépot de fil fondu
L'intégralité du casque anti-bruit est fabriquée par impression 3D, méthode de dépot de fil fondu (Fused Deposition Modeling, FDM).
Dans l'état actuel de sa conception, il demande 300 grammes de PLA et 100 grammes de TPU.
Les matériaux poreux (en PLA ou TPU) ne sont pas modélisés dans la CAO. Ils sont générés dans le logiciel de tranchage à partir de leur contours et de paramètres de motifs de remplissage.
Les matériaux poreux en PLA (image de gauche) sont imprimés directement avec la coque intérieure, avec un taux de remplissage de 25% (75% de porosité) et une hauteur de couche de 250 µm.
Les matériaux poreux en TPU (image de droite) sont imprimés à plat, avec un taux de remplissage de 50 % (50% de porosité) et une hauteur de couche de 250 µm. Le dernier millimètre en hauteur a un taux de remplissage de 10%.
Ces propriétés des matériaux poreux leurs confèrent les propriétés acoustiques adaptées à de leur rôle respectif.
Pour plus d'informations sur la prédiction numérique du comportement acoustique des matériaux poreux réalisés par impression 3D, voir notre article de blog --> https://sil-et-add.fr/des-panneaux-acoustiques-en-semelles-de-chaussures
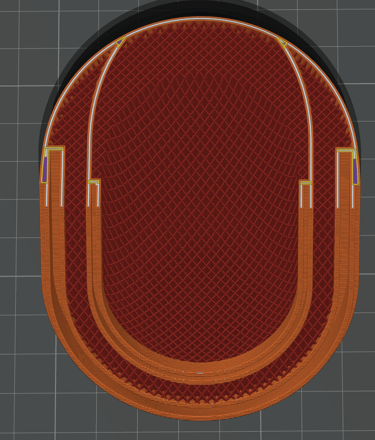
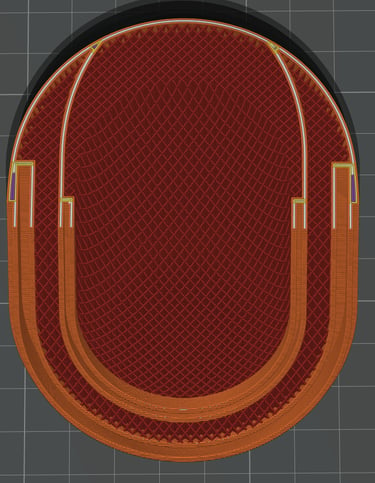
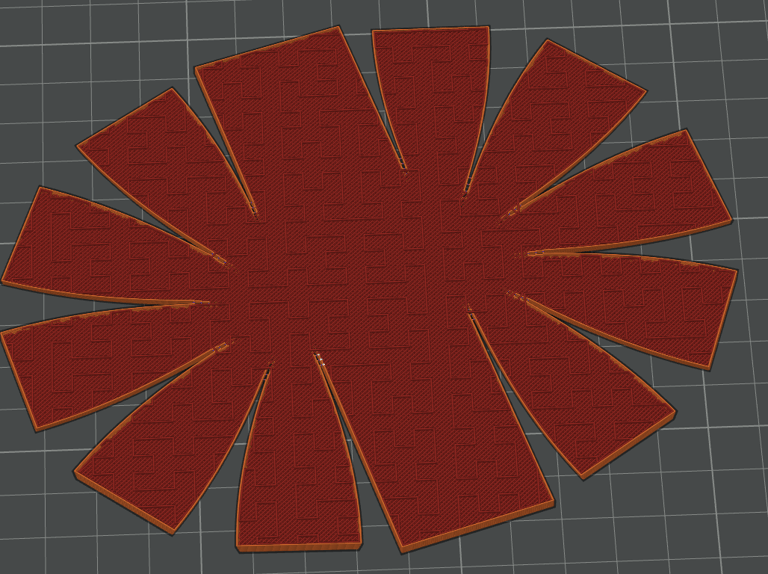
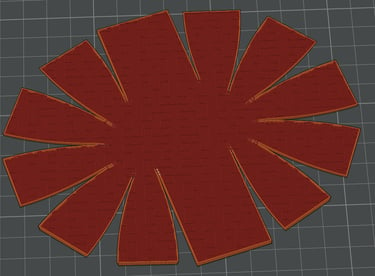
Améliorations
Faites-nous part de vos suggestions d'amélioration via le formulaire de contact dans la section "Contact" du site
Pistes d'amélioration :
Réduire la quantité de TPU nécessaire pour réduire la masse du produit et le coût d'impression 3D : affiner le matériau poreux visco-élastique
Elargir le joint pour améliorer l'étanchéité
Optimiser les dimensions pour réduire la masse du produit et le coût d'impression 3D tout en maximisant l'isolement : épaisseur des coques, des matériaux poreux, taux de remplissage des matériaux poreux - par simulation numérique