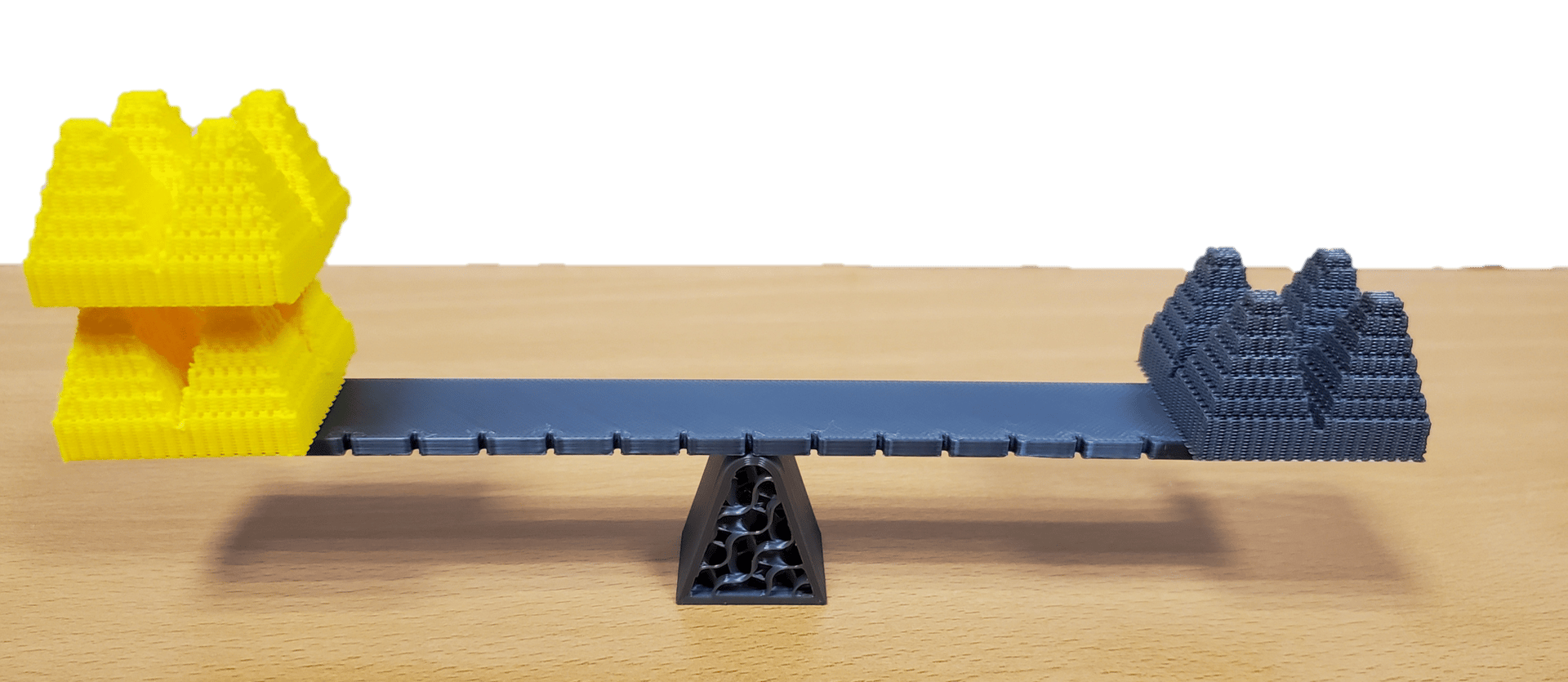
Reducing the weight of 3D-printed acoustic materials
Porous materials, 3D printing, Foaming yarn, Melt deposition, Density, Sound absorption
Jean Boulvert
1/30/20254 min read
3D-printed porous acoustic materials are valued for their customized acoustic performance and mechanical strength. However, they are generally much heavier than conventional porous materials.
This article presents a method for reducing the weight of porous acoustic materials produced by molten wire deposition.
This article is a summary of the presentation given at the AIA International Symposium “Innovative Materials in Acoustics: Between Sustainability and Technology”, Bologna 30th January 2025.
Additive manufacturing is a very useful process for the design and production of acoustic materials and metamaterials. These materials are made up of porous materials, quarter-wave or Helmholtz resonators and membranes. These elements can be dimensioned and arranged to maximize the acoustic performance of the materials.
Additive manufacturing is widely exploited during research and development projects for new acoustic materials, not least because of the following advantages:
Precise control of the microstructure of porous materials, enabling us to design and manufacture customized porous materials, independently of the raw material.
Simplified manufacture of complex structures: simple production of resonators with complex shapes (folding, labyrinthine structures, small dimensions, etc.) filled or not with porous materials.
Combination of elements: resonators tuned to different frequencies or assembled with porous materials.
Rigid porous materials: printed porous materials have a high degree of rigidity, enabling acoustic behavior that is largely independent of the raw material used and of mechanical-acoustic applications.
The figure below shows a non-exhaustive selection of acoustic materials produced by 3D printing.
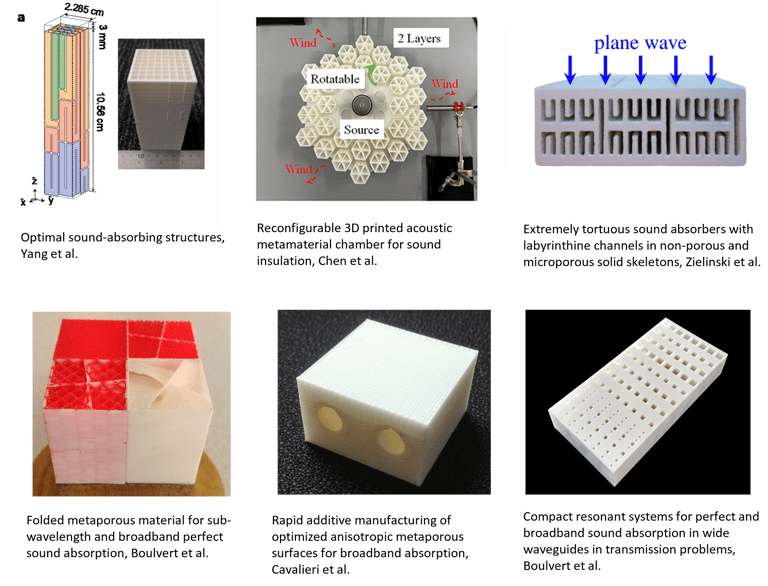
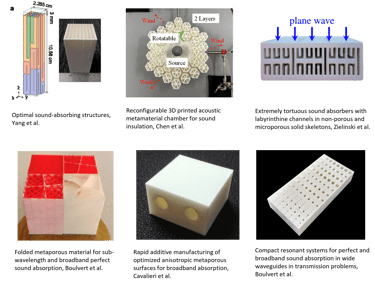
Density of 3D-printed acoustic materials
Although additive manufacturing of acoustic materials offers significant advantages, it also involves constraints, particularly in terms of cost (for large-scale production) and the density of the materials produced.
Density of porous materials
Porous materials are characterized by the shape and size of their pores. For acoustic applications, micro-meshes and triply periodic minimal surface (TPMS) porosity structures are particularly popular. Various 3D printing technologies can be used, such as fused wire deposition (FDM), stereolithography (SLA) and others. In addition, a variety of materials can be used: PLA, PETG, Nylon, resin, etc.
As an example, let's consider a porous micro-mesh material made from PLA by FDM. Its micro-structure is shown in the illustration above on the left and in the photograph (purple material). With an initial PLA density of 1.2 g/cm³ and a nozzle diameter of 400 µm, a 20 mm thick panel requires a porosity of 44% to achieve perfect absorption at its quarter-wave resonance under normal incidence (curve above). It therefore has a density of : 1,2*(1-0,44) = 0,67.
By way of comparison, melamine foam (photograph above, gray material) has a density around 45 times lower.
Density of Helmholtz resonators
When printing Helmholtz resonators using molten wire deposition, it is recommended that the walls be made up of three lines of extruded wire. With a 400 µm nozzle, this gives a wall thickness of 1.2 mm. Still considering PLA, the surface density of the wall is: 1.2 * 1.2 = 1.44 kg/m².
By comparison, an aluminum honeycomb structure with a wall thickness of 100 µm has a surface density of : 2.7 * 0.1 = 0.27 kg/m², i.e. around 5 times less dense than the PLA-printed resonator.
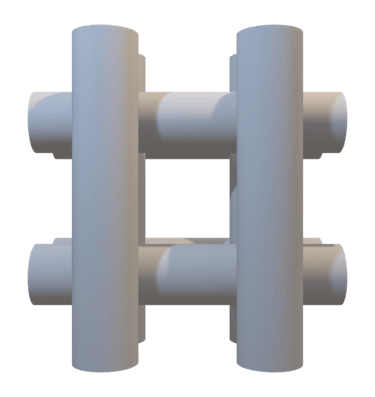
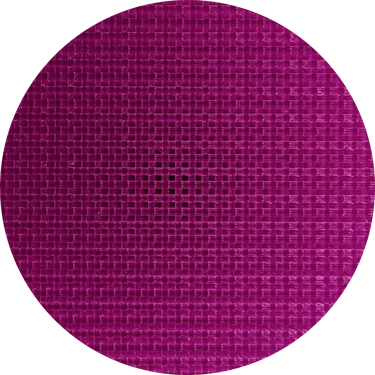
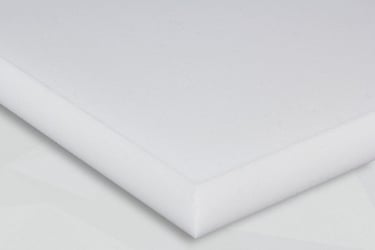
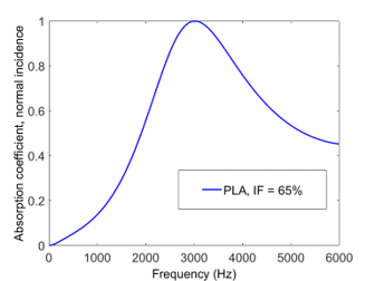
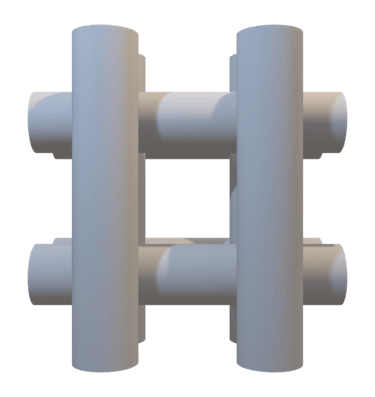
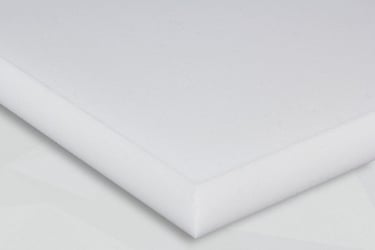
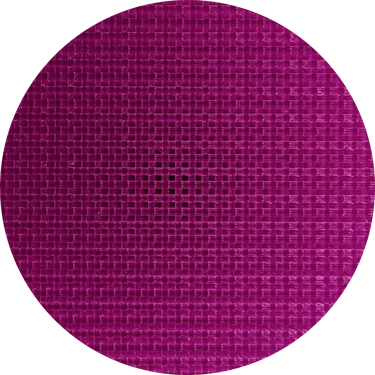
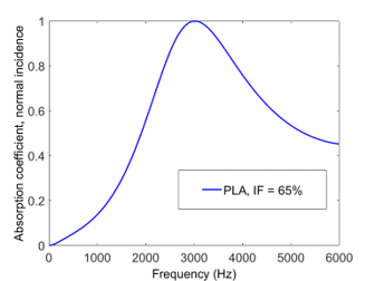
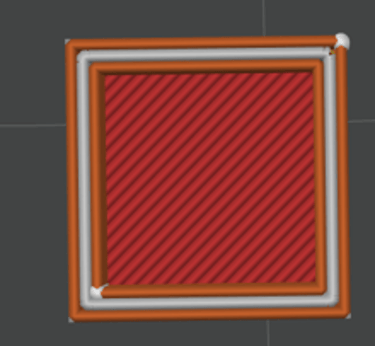
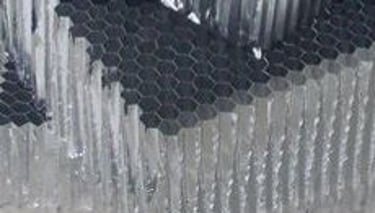
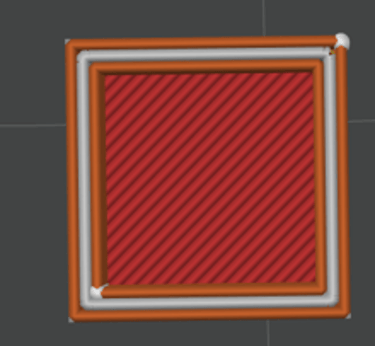
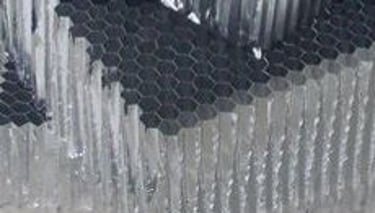
Mass reduction of 3D-printed acoustic materials through the use of foaming yarns
The method presented here for lightening acoustic materials printed by melt deposition involves the use of a foaming filament. Ready-to-use foaming filaments are available, notably in PLA, ASA or TPU. These are known as “light weight” (LW).
The microscope images below show acoustic micro-lattices made by FDM using either a non-foaming yarn (white material) or a foaming fi (yellow material). The width of an extruded wire forming the micro-lattice is around 400 µm.
Changes in mechanical properties as a function of extrusion temperature
Foam yarns contain a thermally activated foaming agent. Activation depends on the extrusion temperature and temperature-related parameters within the extruded filament (flow rate, cooling, etc.). When the yarn foams, pores form inside the yarn, reducing the density of the extruded material compared to a non-foaming yarn. The work of Damanpack et al. illustrates (figures below) the variation in density and mechanical properties as a function of extrusion temperature. At the peak of the foaming effect, the following changes occur in the material:
Reduces density by a factor of 2.5
Young's modulus and yield strength reduced by a factor of 4.
Increased roughness of extruded wires.
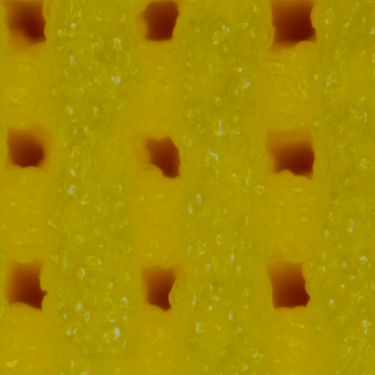
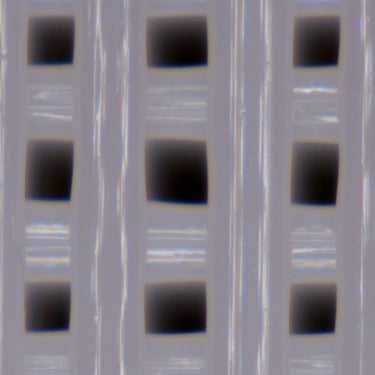
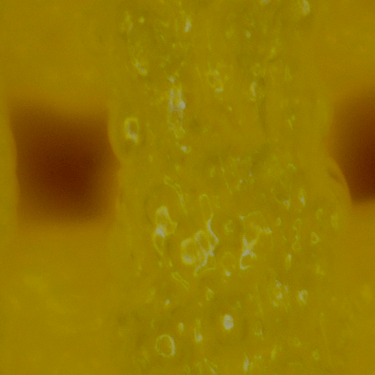
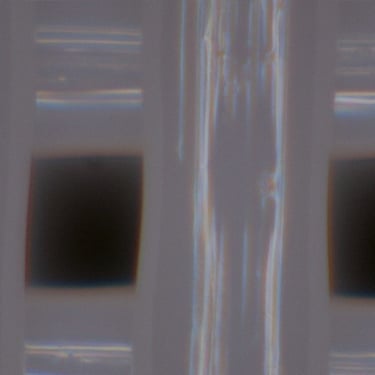
Modification of the acoustic properties of porous materials made with foaming wire
To study the acoustic impact of foaming yarn when used to manufacture porous micro-mesh materials, we produced two sets of micro-mesh samples: one with standard PLA, the other with foaming PLA. The fill density (Infill Factor - IF, the printer parameter controlling the spacing between filaments) was adjusted to obtain a porosity between 90% and 35%. Samples were characterized using impedance tubes to measure their absorption and transmission coefficients at normal incidence. These measurements were also used to determine the equivalent fluid acoustic parameters according to the JCAL model of the micro-trellis as a function of porosity.
The results show that :
The use of foaming yarn does not induce any new acoustic mechanism in the behavior of the micro-mesh. In other words, it continues to behave like a porous material with simple porosity and a rigid skeleton. As a result, the pores inside the wires do not contribute to the overall behavior of the micro-mesh; they are closed. Only the open pores between the filaments contribute.
The use of foam yarn increases the material's tortuosity and slightly reduces the viscous and thermal characteristic lengths. This corresponds to an increase in the intrinsic acoustic losses of the micro-trellis, which is consistent with the rough surface of foamed yarns.
To achieve perfect absorption at quarter-wave resonance, the porosity of a 20 mm thick micro-mesh panel needs to be 48%, compared with 44% with a non-foaming yarn.
The density of the micro-mesh is then : 1.2 / 2.5 * (1-0.48) = 0.25 vs. 0.67 with non-foaming wire.
In conclusion, the use of foaming yarn to produce a porous material by 3D printing makes it possible to divide its density by a factor of at least 2.5, while providing simple acoustic behavior (rigid material with simple acoustic porosity) and reasonably reducing its stiffness and mechanical strength.
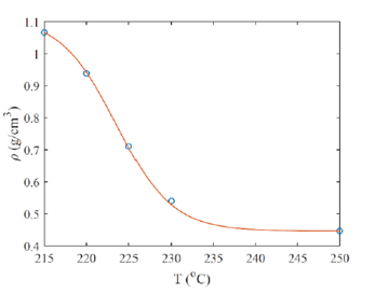
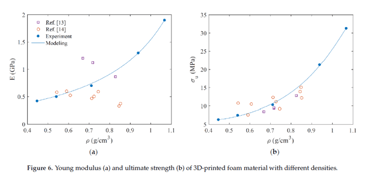
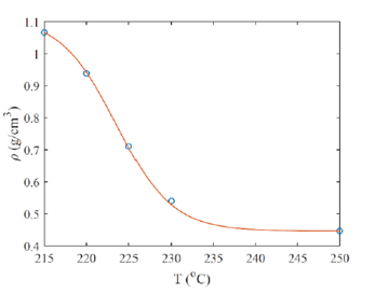
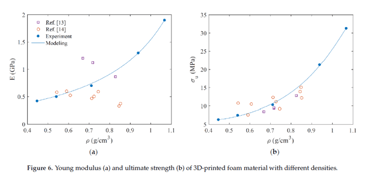
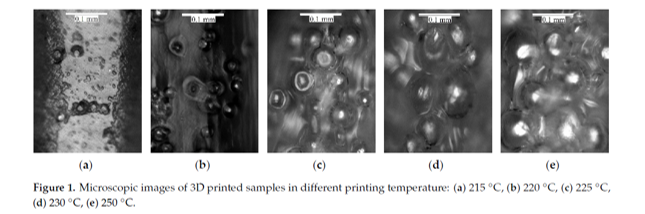
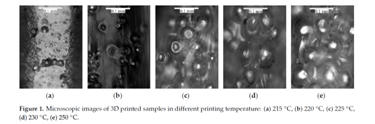
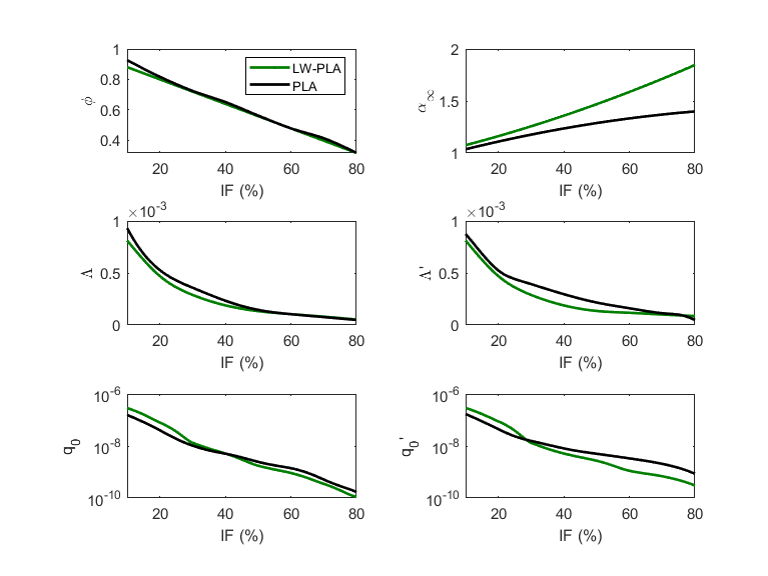
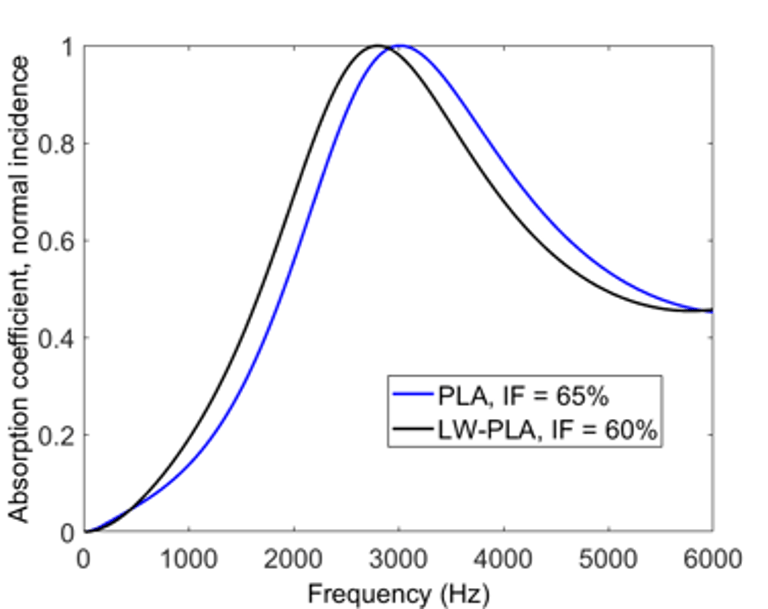
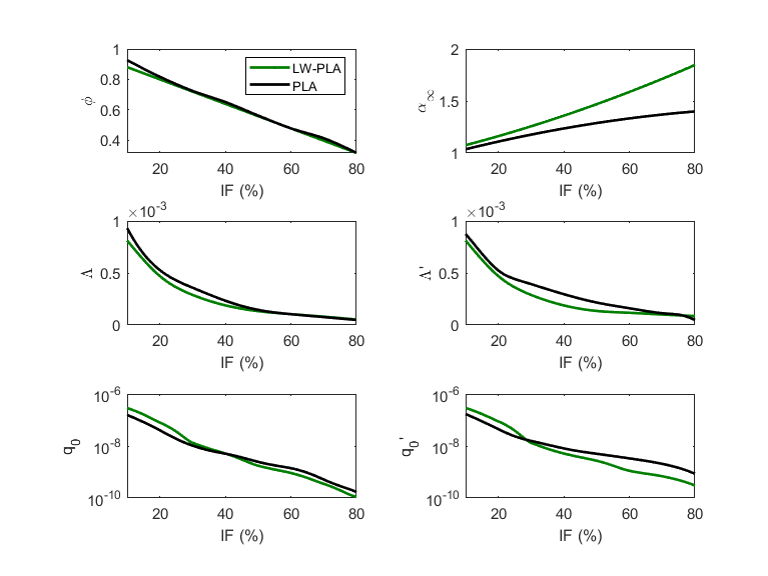
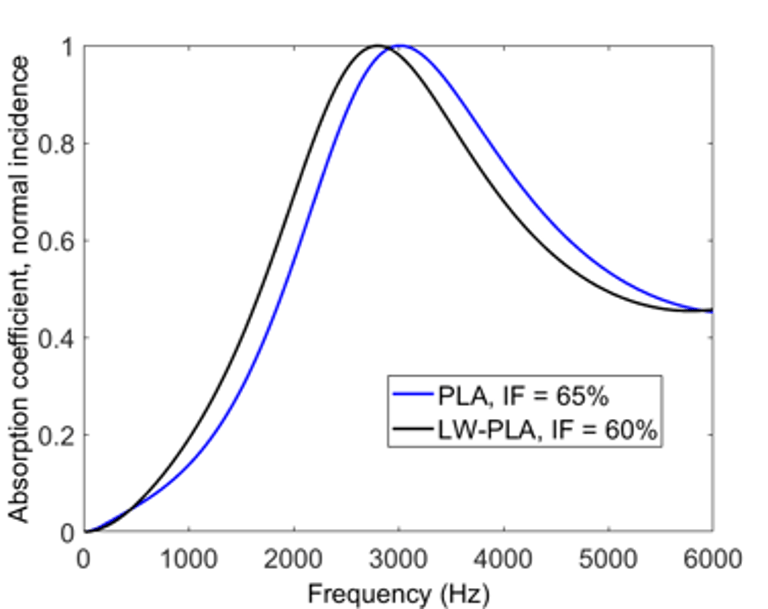
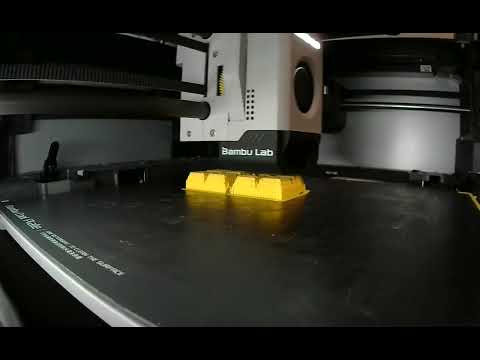